Рихард Бизикс: проект в Лондоне — CASE N3, производство
Итак, это уже мой третий «лондонский кейс». В нем речь пойдет об изготовлении мебели и других элементов необходимых для создания интерьера офиса в столице Туманного Альбиона. Но прежде я кратко напомню, что было, так сказать, в предыдущих сериях.
В первом «кейсе» я рассказал о том, как началась реализация одного из самых уникальных проектов DAVANTI. Полученный опыт оказался эксклюзивным и мы решили поделиться им с обществом. Во втором «кейсе» я рассказывал о том, как вместе с клиентом мы выработали модель осуществления оригинальнейшего замысла. Но параллельно с разработкой плана реализации проекта шел процесс изготовления мебели и других нужных деталей. Эту тему я решил упаковать в отдельный «кейс», поверьте она того заслуживает.
Как я уже говорил, Великобритания страна строгих правил, соблюдать которые нужно, как говориться «от и до». Особенно иностранным компаниям, которые работают на территории Королевства. То есть, малейшее несоответствие нормативам чревато не только санкциями вроде штрафов, но и внесением компании в «черный список». Эта «ведомость» исключает получение разрешения на работу в Англии. Жестко? Зато эффективно и, на мой взгляд, очень правильно.
Одни из самых жестких требований касаются наличия, так называемых, «природных» сертификатов. Они подтверждают, что все используемые в проекте материалы являются экологически чистыми и не представляют угрозы для человека и окружающей среды. Наш проект (за исключение крепежей) полностью выполнялся из натуральной фанеры. Но фанера тоже бывает разной. Нам нужна была гарантия качества и поэтому мы обратились к самому авторитетному в Латвии производителю данного материала – в компанию Latvijas Finieris, специалисты которой прекрасно разбираются в европейских, международных нормативах (к слову, у компании более 15 различных международных сертификатов, включая ISO, CE, BFU, CARB, Powered by Green и др.).
Нами была выбрана березовая фанера. Она является продуктом переработки древесины, ей присущи превосходные физико-механические свойства и выдающееся соотношение показателей массы и механической прочности. В ходе производства все детали пришлось вырезать, обработать их кромку, облицовать и т.п. Обработка всех деталей велась на программируемом фрезерно-сверлильном станке. Добавлю, что при изготовлении панелей использовался клей, соответствие экологическим стандартам которого пришлось подтверждать отдельно.
Чтобы детали можно было запустить в производство, нужно было предоставить планы по расположению мебели, подготовить схемы визуализации и коммуникации и мн.др. Одним словом ввести в курс дела представителей предприятия, дабы у исполнителей нашего заказа была полная картина о проекте.
Производство деталей заняло около двух недель. В целом было изготовлено более сотни сложных элементов из прочной, клееной фанеры. К слову, прочность – одно из ключевых требований. Поскольку, в ходе этого уникального проекта, мебель должна была сформировать не только стеллаж и стенку для хранения офисной «утвари», но и перекрытие, точнее – антресоль, где располагался бы полноценный рабочий кабинет.
Для их транспортировки изготовленных деталей нужно было заказывать грузовой транспорт. Логистику пришлось продумывать вплоть до Лондона – доверить перевозку мы могли только надежным компаниям.
После доставки до места сборки всех этих деталей, естественно, следовал монтаж. Но это уже отдельная тема для разговора. Думаю, справедливым будет посвятить ей отдельный «кейс». На мой взгляд, это один из самых интересных этапов реализации проекта в Лондоне.
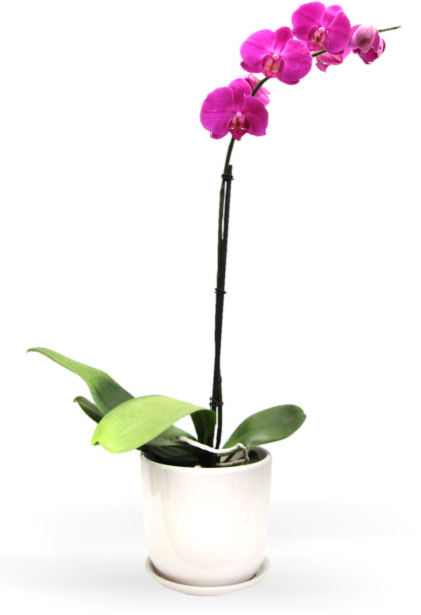